Unlike traditional fabricators, laser profiling companies routinely offer turn-around times measured in days and not weeks. A few are now extending their services to include forming, the tapping of holes, the addition of inserts and even painting in some cases. These secondary operation services however seem to be something of a step into the unknown for many and the results vary somewhat between good and unacceptable. The problems experienced seem to be mostly related to a lack of appreciation of the levels of quality required, care & attention with finish and to on-going quality control.
Without exception, successful fabrication companies have the quality control infrastructure to inspect their work for geometric accuracy, quality of surface finish & de-burring and for missed features such as taped holes. On the contrary, it seems that laser profiling companies just don’t, and what you get is very much a lottery from one order to the next. This is OK if you don’t mind a poor finish, a few burrs and have the facilities to tap any missed holes!
This should really not be a surprise. Over time (and in many cases decades), established fabricators have built teams of skilled personnel and have developed the facilities and procedures that are necessary to consistently deliver the levels of quality that customers have come to expect. It would be naive to expect these fast-turn and low-cost suppliers to deliver the same standards of workmanship and quality. They are likely to need to develop and evolve, invest time and money in quality and perhaps up-skill their work force, by which time they would likely match the fabricators in cost & timescales!
WDS have established relationships with laser profilers to enable them to quickly design & source formed components made from pre-plated material and featuring tapped holes and in some cases inserts such as stand-offs. Delivery times are typically 4 to 7 days, making this ideal for the generation of concept models, early prototypes or lab equipment.
Getting maximum value from laser profiled parts
Like all other manufacturing process, Laser Profiling has its own unique advantages that the designer can exploit to good effect. There are no constraints to profile shape, so acute angles can be cut easily. Curves can be profiled as easily as straights and parts can be “tabbed” so that they are self-jigging on assembly.
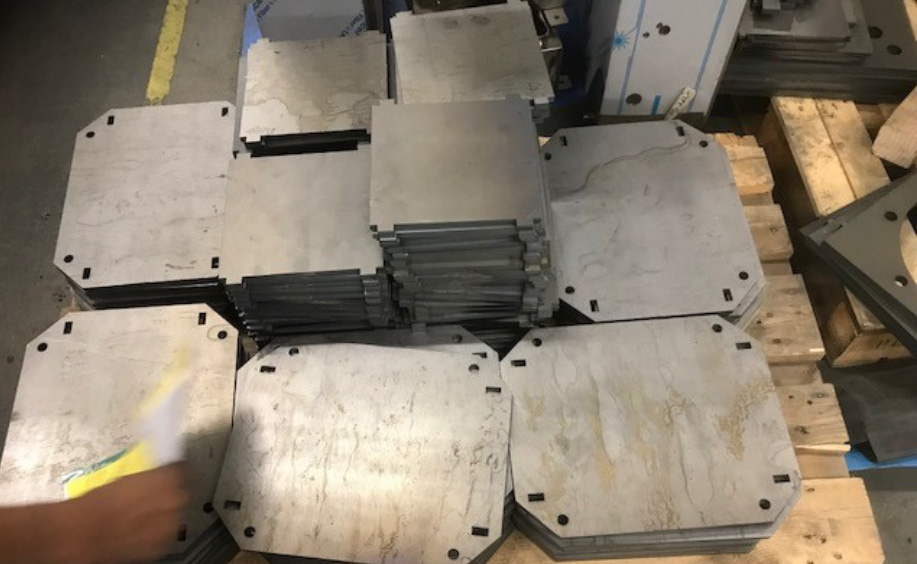
Furthermore, surfaces can be “laser etched” with part numbers or with manufacturing instructions for little additional cost – ideal when there are many similar parts to assemble.
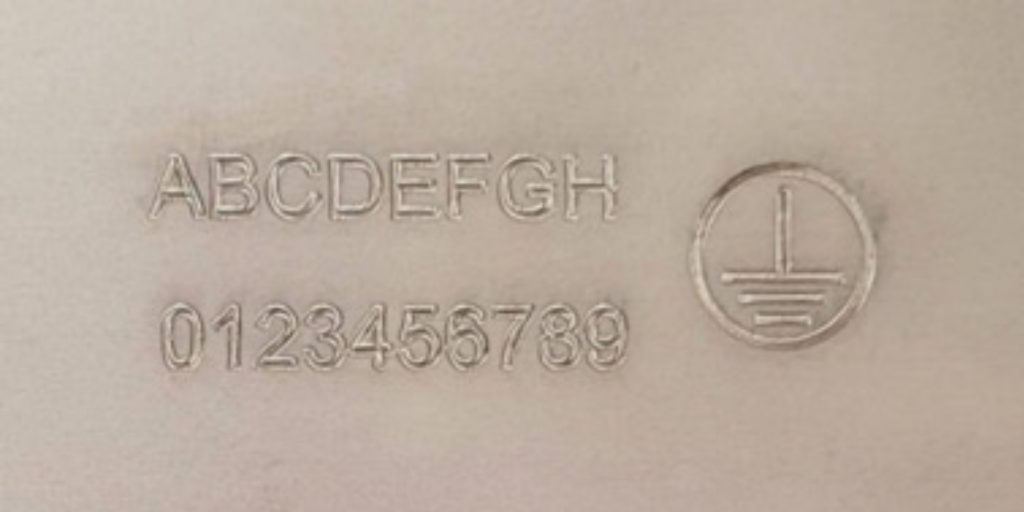
Laser Profiling companies typically hold good stocks of regular mild steel, structural steel, pre-plated steels such as Zintec and stainless steels. Sticking to these materials will ensure the shortest possible lead-times. If appearance, accuracy and quality are critical however, you may need to bite the bullet and engage the services of a company specialising in traditional fabrication services.